Picking en almacén: soluciona los errores más frecuentes
El mundo de la logística se ha visto inmerso en una serie de cambios durante los últimos años. Hoy en día, los procesos en un Centro de Distribución (CEDIS) son muy diferentes a lo que eran antes. Esto trae consigo ciertos retos que, si no se enfrentan de manera correcta, pueden perjudicar tu negocio. Nos dimos a la tarea de investigar y entrevistar a 5 expertos de Netlogistik que cuentan con más de 15 años de experiencia cada uno, para identificar los retos más críticos que enfrenta un CEDIS:
-
La optimización del espacio en un Centro de Distribución.
-
Visibilidad de extremo a extremo en la cadena de suministro.
-
Errores frecuentes en el picking.
-
Nivel de servicio.
-
Información inexacta del inventario.
-
Productividad y talento humano.
En el artículo pasado nos adentramos en el reto de la importancia que tiene la visibilidad en la cadena de suministro. A continuación, te presentamos el tercer reto: errores frecuentes del picking en tu CEDIS. Sigue leyendo para entender el porqué del problema y descubrir los beneficios de solucionarlo con un sistema de gestión de almacenes.
¿Qué es el picking?
Picking es el proceso clave del Centro de Distribución para la preparación de pedidos y determina de manera importante la productividad, la velocidad y la exactitud de tu operación, por lo tanto, afecta de manera directa los costos y el nivel de servicio.
El picking consiste en seleccionar y tomar (pickear) los productos que solicitan nuestros clientes en cada pedido y con un buen sistema de administración de almacenes (WMS) puede realizarse con diversos procesos, los más comunes son:
-
Picking convencional: Tomamos un pedido y recorremos los pasillos del CEDIS para agarrar los productos que se incluyen y al término del recorrido dejamos el pedido en una mesa de empaque o en un andén de embarque. Es un proceso similar al que hacemos cuando vamos de compras al supermercado.
-
Cluster Picking: Tomamos varios pedidos en un carrito o vehículo con compartimientos separados y hacemos un picking convencional, tomando los productos de cada localidad para todos los pedidos que lo requieren y colocando las piezas indicadas en el compartimiento de cada pedido.
-
Picking Inverso o Put to Store: Tenemos localidades definidas para cada pedido o cliente, recorremos los pasillos en un vehículo con uno o más productos y vamos colocando los productos requeridos en la localidad de cada pedido o cliente.
-
Pick and pass: Cuando tenemos un número grande tanto de productos como de presentaciones (SKU por sus siglas en inglés, Single Keeping Unit) y los productos son difíciles de diferenciar entre ellos (por ejemplo en retail farmacéutico) se definen zonas de surtido con un número pequeño de SKUs para ser atendidas por una o pocas personas y así, el contenedor pasa de zona en zona para ser llenado con los productos requeridos por los operadores correspondientes a cada zona.
-
Bulk Picking: Tomamos uno o varios productos de sus localidades correspondientes de manera consolidada para varios pedidos, después colocamos los productos requeridos en localidades destinadas a cada pedido o cliente. Es una combinación de picking convencional y picking inverso.
-
Cruce de Andén: Tomamos los productos en el andén de recibo y los mandamos directamente a ubicaciones destinadas a pedidos o clientes, sin pasar por un área de almacenaje o stock.
Los plazos de entrega requeridos por el mercado son cada vez más cortos y esto requiere una mayor velocidad de procesamiento de pedidos en los centros de distribución y una mayor flexibilidad para atender, con la prioridad adecuada, los pedidos de los clientes, usando la combinación de procesos de picking más adecuada para cada pedido.
¿Cuáles son los principales errores en el picking?
Los errores en los procesos de picking tienen un impacto directo en la productividad y el nivel de servicio del CEDIS y de la cadena de suministro completa, pues si se cometen y no son identificados dentro de las instalaciones, estos se van al cliente generando costos y molestias de alto impacto.
A continuación, te mencionamos algunos de los errores más frecuentes que se cometen durante el picking en almacén:
-
Errores humanos en la selección del producto: al escoger los productos se seleccionan de manera equivocada o en cantidades diferentes a las establecidas en el pedido.
-
Errores humanos en la colocación del producto: al acomodar el producto se hace en una ubicación errónea, de forma tal que el picker o surtidor toma el producto de la ubicación indicada pero el producto es incorrecto. Una falta de organización y control de ubicaciones en el CEDIS, causa que este error se presente de manera frecuente.
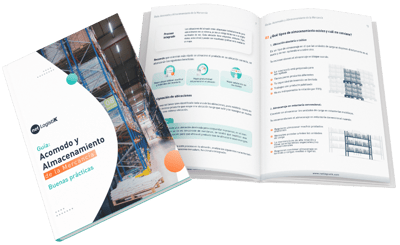
¡Optimiza tu almacén hoy! Descarga sin costo nuestra guía esencial sobre acomodo y almacenamiento de mercancía.
-
El picking se realiza por medio de una lista de papel, lo que da origen a más errores, ya que no se comprueba por medio del sistema que el producto tomado es el correcto.
-
El picking se realiza por varias personas que generan bultos o contenedores diferentes y estos no se consolidan de manera adecuada al momento de empacarlos o embarcarlos.
¿Qué impacto tienen los errores en el picking?
Si tu proceso de picking no es eficiente y no se controla con un sistema, seguramente pondrás una aduana a la salida de tu CEDIS para verificar que el picking haya sido correcto. Este proceso genera costos y tiempos adicionales y no elimina al 100% los errores cometidos. Adicionalmente, por cada error identificado hay un retrabajo de acomodo del producto equivocado con posibles daños al mismo y del picking del producto faltante que debemos buscar de manera independiente para completar el pedido.
Si los errores de picking no son identificados en la “aduana” del CEDIS, hay que sumar los costos de transporte de ida y vuelta del producto considerando el embarque y el proceso completo de logística inversa. Además, un error de mayor impacto es la generación de una mala experiencia de compra con nuestro cliente final, a quien le sobrarán razones para estar molesto.
¿Por qué hay tantos errores en el picking?
Al ser el picking en almacén una actividad que principalmente se realiza con operadores, el problema más fuerte viene cuando el ser humano no conoce los miles de SKU que existen y no puede identificar fácilmente la mercancía a surtir.
Otra problemática con respecto al picking es que los operadores depositan o toman la mercancía de ubicaciones incorrectas, porque no existe un sistema que los ayude a validar dónde la dejan o de qué ubicación la toman.
¿Cómo un WMS me puede ayudar a reducir errores en el picking en almacén?
-
Orienta y dirige al operador con la secuencia lógica en la que debe surtir la mercancía. Esta secuencia debe considerar un slotting o acomodo de mercancía. Con esto, el picking será lo más directo posible a la forma de embarcar y entregar el producto, es decir, hay que empezar por los productos más pesados que van al fondo de una tarima y al final la mercancía más delicada para que no sufra daños.
-
Ayuda al picker a encontrar la mercancía correcta al dirigirse a las localidades de surtido, pues cuando la mercancía está por agotarse, el sistema genera una orden de reabasto para que alguien más apoye a la línea de surtido. Gracias a esto, siempre habrá mercancía y tus procesos serán más eficientes.
-
Asegura que la mercancía que tome el operador sea la correcta, a través de métodos de confirmación como: código de barras, QR, un dígito verificador (en caso de surtir por voz), o luces que señalan la localidad y la cantidad (en caso de surtir por luz).
-
Asegura que el operador coloque la mercancía surtida en el lugar correcto, asignado para el pedido o cliente en cuestión.
-
Ayuda a eliminar el uso del papel, por medio de un dispositivo móvil. Guiará al picker durante todo el proceso y solo podrá cerrarlo cuando el sistema le notifique que finalizó la tarea, por lo que, hay una reducción de errores.
Otro problema común, además de los errores, es que la mercancía se niega al cliente aún y cuando se encuentra en el centro de distribución, pero no se sabe de manera clara en qué localidad está, por lo que, al no surtir ese pedido, quedan mal con la promesa de entrega previamente establecida con el cliente.
Explora todos los secretos para elegir y aprovechar al máximo los sistemas de gestión de almacenes.
En conclusión, un WMS ayuda a:
-
Que el operador no tenga que esperar al supervisor para que se le asignen tareas.
-
Que el operador recorra la menor distancia posible para surtir los pedidos que le corresponden.
-
Que los pedidos se procesen en menos tiempo y los que sean críticos por nivel de servicio o destino final, sean atendidos de manera prioritaria, cumpliendo así los niveles de servicio, promesa de compra y de entrega.
-
Que la mercancía en el CEDIS sea surtida al cliente final o a la tienda con puntualidad y sin errores.
Recuerda que disminuir los errores del picking en almacén, te ayudará a aumentar la calidad del servicio brindado a tu cliente final.
¡Síguenos en LinkedIn para mantenerte informado de contenido relacionado!